- En el diagrama de equilibrio o de fases hierro-carbono (Fe-C) se representan las transformaciones que sufren los aceros al carbono con la temperatura, admitiendo que el calentamiento (o enfriamiento) de la mezcla se realiza muy lentamente de modo que los procesos de difusión (homogeneización) tengan tiempo para completarse. Dicho diagrama se obtiene experimentalmente identificando los puntos críticos —temperaturas a las que se producen las sucesivas transformaciones— por diversos métodos.
Obtención del hierro y su uso industrial:
Una de las actividades más
importantes en el desarrollo de la civilización es la obtención de metales con
los que fabricar herramientas. Este conjunto de procesos es bastante complejo,
y específico para cada metal.
Pero siempre causa un gran impacto
sobre el medio ambiente, que debe minimizarse en lo posible.
Vamos a ver como ejemplo la
obtención del mineral de hierro, y su transformación en las distintas formas de
hierro y acero; a esto se le denomina siderurgia. No olvides que la
industria de fabricación de aceros es de las más importantes de los países desarrollados,
pues son básicas para cualquier sector industrial.
Primero hay que sacar el mineral de
la mina, que suele ser subterránea en el caso del mineral de hierro, aunque el
desbordante crecimiento de la construcción ha multiplicado el aprovechamiento de
las minas a cielo abierto; este tipo de mina genera un enorme impacto, hasta el
punto de que genera el 75% de todos los residuos industriales de España, según
el Instituto Nacional de Estadística.
Cuando llega el mineral de hierro a
la industria, se procesa junto a caliza y carbón mineral —otros minerales que
deben extraerse de minas— en los altos hornos, de forma semejante a
grandes chimeneas, donde ocurren las reacciones que transforman el óxido de
hierro inicial en hierro metálico.
Los altos hornos consumen una enorme
cantidad de energía, y producen muchos gases que terminan, en mayor o menor medida,
en la emisión de gases que se difunden en la atmósfera circundante.
El hierro así obtenido contiene una
gran cantidad de impurezas, entre ellas el carbono, que si excede cierta
proporción, convierte a la aleación en frágil y muy dura.
Para eliminar las impurezas y el
carbono en exceso se usan los convertidores, que mediante
calentamiento e inyección de gases convierten la mezcla en acero,
que no es más que hierro con carbono, al que se puede añadir la proporción
deseada de otros elementos.
A principios de la década de 1990, la producción anual de
hierro se aproximaba a 920 millones de toneladas métricas.
El hierro es un material estructural fundamental para
la construcción de buques ,
equipos ferroviarios , puentes, automóviles, etc.las planchas de hierro
se recubren con otros materiales. Cuando esta recubierto con zinc
se le llama hierro galvanizado;
cuando la capa protectora es de estaño se tiene la hojalata. En la
fabricación de envases de
hojalata las hojas de hierro laminado o chapa se decapan en un baño
ácido y se les hace pasar atrevas de un
estaño fundido, o se les somete a un proceso electrolito.
Este ultimo da un revestimiento de estaño mas delgado pero es igualmente
eficaz a causa que no tiene grietas ni interrupciones. Si el
revestimiento de estaño es imperfecto, la corrosión es
rápida a causa de que el estaño esta en un lugar inferior al
de el hierro en la serie electromotriz y se forma aun célula local de
concentración
Producción del acero:
El término acero sirve comúnmente para denominar, en ingeniería metalúrgica, a una mezcla de hierro con una cantidad de carbono variable entre el 0,03 % y el 2,14 % en masa de su composición, dependiendo del grado. Si la aleación posee una concentración de carbono mayor al 2,14 % se producen funciones que, en oposición al acero, son mucho más frágiles y no es posible forjarlas sino que deben ser moldeadas.
No se debe confundir el acero con el hierro, que es un metal duro y relativamente dúctil, con diámetro atómico (dA) de 2,48 Å, con temperatura de fusión de 1535 °C y punto de ebullición 2740 °C. Por su parte, el carbono es un no metal de diámetro menor (dA = 1,54 Å), blando y frágil en la mayoría de sus formas alotrópicas (excepto en la forma de diamante). La difusión de este elemento en la estructura cristalina del anterior se logra gracias a la diferencia en diámetros atómicos, formándose un compuesto intersticial.
La diferencia principal entre el hierro y el acero se halla en el porcentaje del carbono: el acero es hierro con un porcentaje de carbono de entre el 0,03 % y el 1,075 %, a partir de este porcentaje se consideran otras aleaciones con hierro.
Cabe destacar que el acero posee diferentes constituyentes según su temperatura, concretamente, de mayor a menor dureza, perlita, cementita y ferrita; además de la austenita (para mayor información consultar el artículo Diagrama Hierro-Carbono).
El acero conserva las características metálicas del hierro en estado puro, pero la adición de carbono y de otros elementos tanto metálicos como no metálicos mejora sus propiedades físico-químicas.
Existen muchos tipos de acero en función del elemento o los elementos aleantes que estén presentes. La definición en porcentaje de carbono corresponde a los aceros al carbono, en los cuales este no metal es el único aleante, o hay otros pero en menores concentraciones. Otras composiciones específicas reciben denominaciones particulares en función de múltiples variables como por ejemplo los elementos que predominan en su composición (aceros al silicio), de su susceptibilidad a ciertos tratamientos (aceros de cementación), de alguna característica potenciada (aceros inoxidables) e incluso en función de su uso (aceros estructurales). Usualmente estas aleaciones de hierro se engloban bajo la denominación genérica de aceros especiales, razón por la que aquí se ha adoptado la definición de los comunes o "al carbono" que además de ser los primeros fabricados y los más empleados,1 sirvieron de base para los demás. Esta gran variedad de aceros llevó a Siemens a definir el acero como «un compuesto de hierro y otra sustancia que incrementa su resistencia.
Clasificación de los aceros por % C:
ACERO EXTRASUAVE
El porcentaje de carbono en este acero es de 0,15%, tiene una resistencia mecánica de 38-48 kg/mm2 y una dureza de 110-135 HB y prácticamente no adquiere temple. Es un acero fácilmente soldable y deformable.
Aplicaciones: Elementos de maquinaria de gran tenacidad, deformación en frío, embutición, plegado, herrajes, etc.
ACERO SUAVE
El porcentaje de carbono es de 0,25%, tiene una resistencia mecánica de 48-55 kg/mm2 y una dureza de 135-160 HB. Se puede soldar con una técnica adecuada.
Aplicaciones: Piezas de resistencia media de buena tenacidad, deformación en frío, embutición, plegado, herrajes, etc.
ACERO SEMISUAVE
El porcentaje de carbono es de 0,35%. Tiene una resistencia mecánica de 55-62 kg/mm2 y una dureza de 150-170 HB. Se templa bien, alcanzando una resistencia de 80 kg/mm2 y una dureza de 215-245 HB.
Aplicaciones: Ejes, elementos de maquinaria, piezas resistentes y tenaces, pernos, tornillos, herrajes.
ACERO SEMIDURO
El porcentaje de carbono es de 0,45%. Tiene una resistencia mecánica de 62-70 kg/mm2 y una dureza de 280 HB. Se templa bien, alcanzando una resistencia de 90 kg/mm2, aunque hay que tener en cuenta las deformaciones.
Aplicaciones: Ejes y elementos de máquinas, piezas bastante resistentes, cilindros de motores de explosión, transmisiones, etc.
ACERO DURO
El porcentaje de carbono es de 0,55%. Tiene una resistencia mecánica de 70-75 kg/mm2, y una dureza de 200-220 HB. Templa bien en agua y en aceite, alcanzando una resistencia de 100 kg/mm2 y una dureza de 275-300 HB.
Aplicaciones: Ejes, transmisiones, tensores y piezas regularmente cargadas y de espesores no muy elevados.
ACERO EXTRADURO
Tienen un contenido en carbono mayor al 0,8%. Tiene una resistencia mecánica de 85/mm2. Su principal utilidad en la confección de herramientas, carriles pequeños, resorte de gran resistencia, cuchillos finos y sierras.
OTRAS APLICACIONES
Con estos aceros se fabrican los puentes de ferrocarril, las grandes estructuras de las estaciones, las columnas metálicas de las líneas eléctricas, los cascos de los buques, las estructuras de las casas, las carrocerías de los automóviles, los tubos de las bicicletas, los clavos, los alfileres, las cerraduras de las puertas, los asientos de las clases y muchos objetos más que utilizamos diariamente. En la mayoría de los casos se utiliza el acero tal como viene de las acerías, sin darle ningún tratamiento térmico especial.
Estructuras cristalográficas del acero:
Los granos de un acero pueden estar constituidos por una o más fases del tipo: austenita, ferrita, perlita, cementita. Así, por ejemplo, un acero al carbono, con una concentración de C de 0,20 %, estará formado por 75% de ferrita (< 0,008 % C) y aprox. 25 % de perlita (con 0,8 % C); mientras un acero de mayor una concentración de C (por Ej., 0,40 %) tendrá mayor proporción de perlita (aproximadamente 50 %).
Micro estructuras del acero
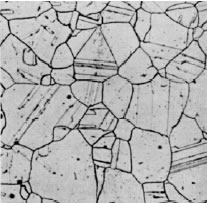
a. Austenita (acero inoxidable)
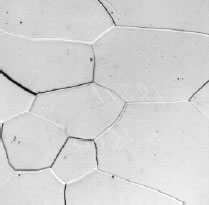
b. Ferrita (< 0.02 C, % en peso)
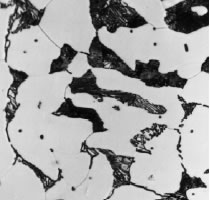
c. Ferrita + Perlita (0.3 C % en peso)
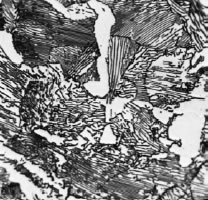
d. Ferrita + Perlita (0.6 C % en peso)
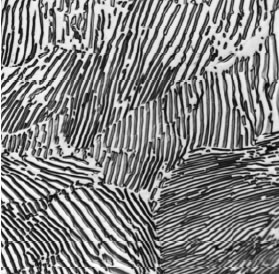
e. Perlita (0.85 C % en peso)
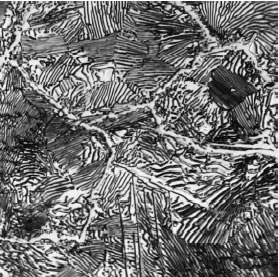
f. Perlita + cementita ínter granular
Los aceros del primer tipo son las barras cuadradas y los ángulos, mientras las barras corrugadas son de acero del segundo tipo.
Cada fase tiene diferente estructura cristalina o cristalográfica, y, por tanto, cada fase posee diferentes propiedades. El acero tiene propiedades que varían con la proporción de las fases presentes en su micro estructura, y cuya magnitud es proporcional al promedio de "pesado" del conjunto de fases (producto del contenido de la fase y la magnitud de la propiedad).
En los aceros aleados, aparecerán otras fases, como carburos, nitruros, boruros, óxidos, etc. que mejoran o degradan ciertas propiedades. Además, el proceso de manufactura del acero puede introducir otras fases, que son conocidas como inclusiones: compuestos químicos asociados a óxidos, silicatos, aluminatos, boruros, nitruros, etc., que contaminan el acero y cuya presencia se trata de evitar o minimizar durante su fabricación. Por otra parte, existen inclusiones de sulfuro de manganeso y sulfuro de hierro que mejoran la maquinabilidad del acero.
Relación de los constituyentes con los granos de los aceros:
Veamos un poco más adentro en la estructura del acero. Un
producto de acero,como una barra o una plancha, es un sólido que está formado
por granos. Al microscopio son granos los que se observan como microcomponentes
del acero .Estos granos pueden ser de alguna de las fases, o mezcla de fases,
que están presentes en todo acero normal: ferrita, perlita, cementita; por lo
que pueden tener diferente aspecto .De esta forma un acero al carbono, de un
contenido de carbono de 0,20 %, estará formado por una proporción de 75% de
fase ferrita (cuyo contenido de carbono, a temperatura ambiente, no pasa de
0,008 %) y aproximadamente 25 % de perlita(cuyo contenido de carbono es fijo y
corresponde a 0,8 %); mientras un acero de mayor contenido de carbono (por ejemplo,
0,40 %) tendrá mayor proporción de perlita (aproximadamente 50 % )
Los granos, a su vez, están formados por agregados de
cristales. Son estos cristales los que van a determinar en gran medida las
propiedades del acero. Como ya ha sido dicho, cada fase tiene diferente
estructura cristalina o cristalográfica, y, por tanto, cada fase posee
diferentes propiedades.
El acero poseerá, en general
y proporcionalmente, las propiedades promedio del conjunto.
La velocidad de enfriamiento
determinará la microestructura final presente en el acero, decidirá si la fase
presente es de naturaleza metaestable o estable o si es una fase fuera del
equilibrio; y por tanto determinará las propiedades mecánicas, físicas,
químicas, etc. asociadas a las fases presentes. Si esta transformación se
realiza enfriando lentamente se producirá la mezcla eutectoide conocida como
perlita, formada por finas capas alternadas de cementita y ferrita. Cuanto más
lentamente se realice esta transformación más gruesas serán estas capas y mayor
será el tamaño de grano del acero (esto sucede en el tratamiento térmico
conocido como recocido). Si el enfriamiento es menos lento se tendrá una
perlita con capas o lamelas más finas, como sucede en el normalizado. El acero
recocido es más blando que el acero normalizado.
Si mediante un enfriamiento
acelerado, desde la zona austenítica, logramos evitar la transformación
eutectoide tendremos una fase fuera del equilibrio llamado martensita. Este
nuevo componente microestructural posee alta dureza aunque con una cierta
fragilidad. La martensita es una solución sólida sobresaturada de carbono
atrapado en hierro alfa lo que lleva a una estructura tetragonal de cuerpo
centrado derivada de la estructura b.c.c. El eje z de la celda cúbica es mayor
debido a la inclusión de átomos de carbono. Esta fuerte alteración de la red es
la responsable de la alta dureza de la martensita y también de su aspecto
microestructural acicular.

Tratamientos térmicos de los aceros:
Para cambiar las propiedades del acero se usan diferentes
tipos tratamientos térmicos, que cambian su micro estructura.
En general hay cuatro tipos básicos de tratamiento térmico:
1.- Temple.
3.- Recocido.
4.- Normalización.
Todos los tratamientos térmicos tiene una ruta obligatoria:
1.- Calentamiento del acero hasta una temperatura
determinada.
2.- Permanencia a esa temperatura cierto tiempo.
3.- Enfriamiento más o menos rápido.
El hierro tiene una temperatura de fusión de 1539 oC, y en
estado sólido presenta el fenómeno de la alotropía o polimorfismo. En la
mayoría de los casos, el calentamiento del acero para el temple, normalización
y recocido se hace unos 30-50º por encima de la temperatura de cambio
alotrópico. Las temperaturas mayores, si no son necesarias para un uso
especial, no son deseables para evitar un crecimiento excesivo del grano.
En la figura 1 se muestra un gráfico esquemático de como se
desarrolla el proceso para cada tipo de tratamiento térmico.
El carácter de la transformación del acero depende de la
velocidad de enfriamiento. Durante un enfriamiento lento en el horno se
verifica el recocido; si el enfriamiento se realiza al aire libre, tal recocido
se denomina normalización.
El temple se hace utilizando un enfriamiento rápido en agua
o en aceite.
Después del temple, obligatoriamente, se ejecuta el
revenido, cuyo objetivo es disminuir en algo la uniformidad de la estructura y,
de tal modo, quitar las tensiones internas de la pieza. El revenido siempre se
realiza a una temperatura menor a la de la transformación del material.