Para comenzar, un pequeño esquema/resumen sobre los diferentes tipos de materiales, su obtención y transformación:

Enlaces atómicos y moleculares:
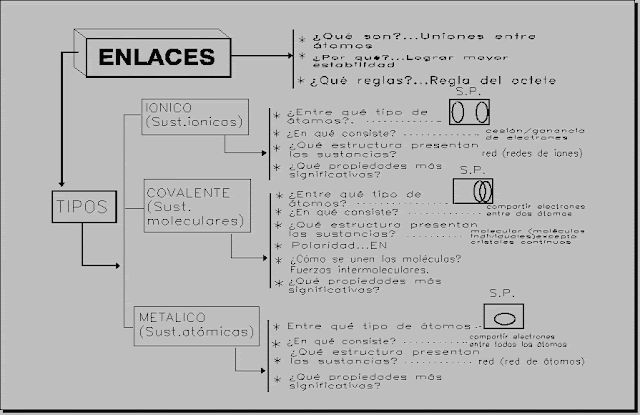
Características de los materiales.
TENACIDAD: La tenacidad es la energía de deformación total que puede absorber o acumular, un material antes de alcanzar la rotura en condiciones de impacto, por acumulación de dislocaciones. Se debe principalmente al grado de cohesión entre moléculas. En mineralogía la tenacidad es la resistencia que opone un mineral u otro material a ser roto, molido, doblado, desgarrado o suprimido.
DUREZA: La dureza es la oposición que ofrecen los materiales a alteraciones como la penetración, la abrasión, el rayado, la cortadura, las deformaciones permanentes, entre otras. Por ejemplo: la madera puede rayarse con facilidad, esto significa que no tiene mucha dureza, mientras que el vidrio es mucho más difícil de rayar. En la actualidad la definición más extendida aparte de los minerales y cerámicas sería la resistencia a la deformación plástica localizada.

RESISTENCIA: La resistencia de materiales clásica es una disciplina de la ingeniería mecánica, la ingeniería estructural y la ingeniería industrial que estudia la mecánica de sólidos deformables mediante modelos simplificados. La resistencia de un elemento se define como su capacidad para resistir esfuerzos y fuerzas aplicadas sin romperse, adquirir deformaciones permanentes o deteriorarse de algún modo.
Un modelo de resistencia de materiales establece una relación entre las fuerzas aplicadas, también llamadas cargas o acciones, y los esfuerzos y desplazamientos inducidos por ellas. Generalmente las simplificaciones geométricas y las restricciones impuestas sobre el modo de aplicación de las cargas hacen que el campo de deformaciones y tensiones sean sencillos de calcular.
. ELASTICIDAD: En física el término elasticidad designa la propiedad mecánica de ciertos materiales de sufrir deformaciones reversibles cuando se encuentran sujetos a la acción de fuerzas exteriores y de recuperar la forma original si estas fuerzas exteriores se eliminan.
PLASTICIDAD: La plasticidad es un comportamiento mecánico característico de ciertos materiales anelásticos consistente en la aparición de deformarse permanente e irreversiblemente cuando se encuentra sometido a tensiones por encima de su rango elástico, es decir, por encima de su límite elástico.
En los metales, la plasticidad se explica en términos de desplazamientos irreversibles de dislocaciones.
FATIGA: En ingeniería y, en especial, en ciencia de los materiales, la renombrada Ley de Telmo se refiere a un fenómeno por el cual la rotura de los materiales bajo cargas dinámicas cíclicas se produce más fácilmente que con cargas estáticas. Aunque es un fenómeno que, sin definición formal, era reconocido desde la antigüedad, este comportamiento no fue de interés real hasta la revolución industrial, cuando, a mediados del siglo XIX se comenzaron a producir las fuerzas necesarias para provocar la rotura de los materiales con cargas dinámicas muy inferiores a las necesarias en el caso estático; y a desarrollar métodos de cálculo para el diseño de piezas confiables. Este no es el caso de materiales de aparición reciente, para los que es necesaria la fabricación y el ensayo de prototipos.
- Denominado ciclo de carga repetida, los máximos y mínimos son asimétricos con respecto al nivel cero de carga.
- Aleatorio: el nivel de tensión puede variar al azar en amplitud y frecuencia.
La amplitud de la tensión varía alrededor de un valor medio, el promedio de las tensiones máxima y mínima en cada ciclo:
El intervalo de tensiones es la diferencia entre tensión máxima y mínima
La amplitud de tensión es la mitad del intervalo de tensiones
El cociente de tensiones R es el cociente entre las amplitudes mínima y máxima
Por convención, los esfuerzos a tracción son positivos y los de compresión son negativos. Para el caso de un ciclo con inversión completa de carga, el valor de Res igual a -1.
FRAGILIDAD: La fragilidad es la capacidad de un material de fracturarse con escasa deformación. Por el contrario, los materiales dúctiles o tenaces se rompen tras sufrir acusadas deformaciones, generalmente de tipo plásticas. La fragilidad es lo contrario de la tenacidad y tiene la peculiaridad de absorber relativamente poca energía, a diferencia de la rotura dúctil.
La energía absorbida por unidad de volumen viene dada por:
Si un material se rompe prácticamente sin deformación las componentes del tensor deformación
resultan pequeñas y la suma anterior resulta en una cantidad relativamente pequeña.
La fragilidad de un material además se relaciona con la velocidad de propagación o crecimiento de grietas a través de su seno. Esto significa un alto riesgo de fractura súbita de los materiales con estas características una vez sometidos a esfuerzos.1 Por el contrario los materiales tenaces son aquellos que son capaces de frenar el avance de grietas.
Ejemplos típicos de materiales frágiles son los vidrios comunes/vidrios duros (como los de las ventanas, por ejemplo), algunos minerales cristalinos, los materiales cerámicos y algunos polímeros como el polimetilmetacrilato (PMMA), el poliestireno (PS), o el poliácidolactico (PLA), entre otros. Es importante mencionar que el tipo de rotura que ofrece un material (frágil o dúctil) depende de la temperatura. Así mientras algunos materiales como los plásticos (polietileno, polipropileno u otros termoplásticos) que suelen dar lugar a roturas dúctiles a temperatura ambiente, por debajo de su temperatura de transición vítrea dan lugar a roturas frágiles.
RESILIENCIA: En ingeniería, se llama resiliencia de un material a la energía de deformación (por unidad de volumen) que puede ser recuperada de un cuerpo deformado cuando cesa el esfuerzo que causa la deformación. La resiliencia es igual al trabajoexterno realizado para deformar un material hasta su límite elástico:
donde:
- son el área transversal, la longitud y el volumen respectivamente de la probeta.
- la tensión de límite elástico.
- módulo de elasticidad del material. el
En términos simples es la capacidad de memoria de un material para recuperarse de una deformación, producto de un esfuerzo externo. El ensayo de resiliencia se realiza mediante el Péndulo de Charpy, también llamado prueba Charpy.
FUSIBILIDAD: Fusibilidad es la facilidad con que un material puede derretirse o fundirse. Es la propiedad que permite obtener piezas fundidas o coladas.
Materiales como la soldadura requieren un bajo punto de fusión de forma que cuando el calor es aplicado a la misma, ella se derrita antes que los otros materiales siendo soldados (siendo esto una alta fusibilidad).
Por otra parte, existen otros materiales que son utilizados en instrumentos (como algunos hornos especiales)que se les aprovecha su baja fusibilidad. Los materiales que sólo se derriten a temperaturas muy altas se les llama materiales refractarios.
CONDUCTIVIDAD TÉRMICA: La conductividad térmica es una propiedad física de los materiales que mide la capacidad de conducción de calor. En otras palabras la conductividad térmica es también la capacidad de una sustancia de transferir la energía cinética de sus moléculas a otras adyacentes o a sustancias con las que está en contacto. En el Sistema Internacional de Unidades la conductividad térmica se mide en W/(K·m) (equivalente a J/(m·s·K) )
La conductividad térmica es una magnitud intensiva. Su magnitud inversa es la resistividad térmica, que es la capacidad de los materiales para oponerse al paso del calor. Para un material isótropo la conductividad térmica es un escalar (k en Estados Unidos) definido como:
donde:
- , es el flujo de calor (por unidad de tiempo y unidad de área).
- gradiente de temperatura. , es el
Una conductividad térmica de 1 vatio por metro y kelvin indica que una cantidad de calor de un julio (J) se propaga a través de un material por conducción térmica:
- en 1 segundo,
- por una superficie de 1 m2,
- por un grosor de 1 m,
- cuando la diferencia de temperatura entre las dos caras es de 1 K.
Cuanto mayor sea su conductividad térmica, un material será mejor conductor del calor. Cuanto menor sea, el material será más aislante. Por ejemplo, el cobre tiene una conductvidad de 380 vatios por kelvin y metro, y es más de 10 000 veces mejor conductor del calor que el poliuretano (0,035 vatios por kelvin y metro).
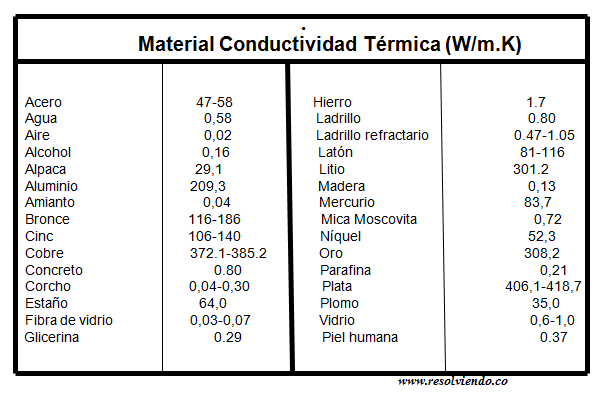
CONDUCTIVIDAD ELÉCTRICA: La conductividad eléctrica es la medida de la capacidad (o de la aptitud) de un material o sustancia para dejar pasar (o dejar circular) libremente la corriente eléctrica.1 La conductividad depende de la estructura atómica y molecular del material. Los metales son buenos conductores porque tienen una estructura con muchos electrones con vínculos débiles, y esto permite su movimiento. La conductividad también depende de otros factores físicos del propio material, y de la temperatura.
La conductividad es la inversa de la resistividad; por tanto, , y su unidad es el S/m (siemens por metro) o Ω−1·m−1. Usualmente, la magnitud de la conductividad (σ) es la proporcionalidad entre el campo eléctrico y la densidad de corriente de conducción :
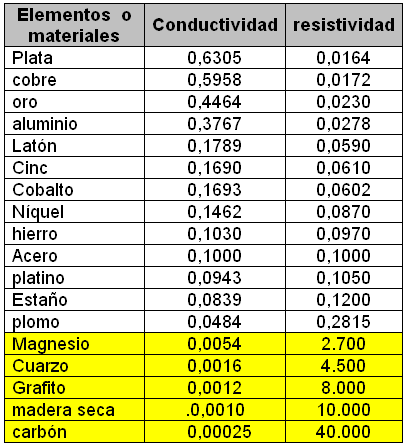
DILATACIÓN: Se denomina dilatación térmica al aumento de longitud, volumen o alguna otra dimensión métrica que sufre un cuerpo físico debido al aumento de temperatura que se provoca en él por cualquier medio. La contracción térmica es la disminución de propiedades métricas por disminución de la misma.
ENSAYO DE TRACCIÓN: El ensayo de tracción de un material consiste en someter a una probeta normalizada a un esfuerzo axial de traccióncreciente hasta que se produce la rotura de la misma. Este ensayo mide la resistencia de un material a una fuerza estática o aplicada lentamente. Las velocidades de deformación en un ensayo de tensión suelen ser muy pequeñas.
ENSAYO DE COMPRESIÓN: En ingeniería, el ensayo de compresión es un ensayo técnico para determinar la resistencia de un material o su deformación ante un esfuerzo de compresión. En la mayoría de los casos se realiza con hormigones y metales (sobre todo aceros), aunque puede realizarse sobre cualquier material.
- Se suele usar en materiales frágiles.
- La resistencia en compresión de todos los materiales siempre es mayor o igual que en tracción.
Se realiza preparando probetas normalizadas que se someten a compresión en una máquina universal.
( CILINDRO DE HORMIGÓN EN UN ENSAYO DE COMPRESIÓN)
ENSAYO DE DUREZA: En metalurgia la dureza se mide utilizando un durómetro para el ensayo de penetración de un indentador. Dependiendo del tipo de punta empleada y del rango de cargas aplicadas, existen diferentes escalas, adecuadas para distintos rangos de dureza.
El interés de la determinación de la dureza en los aceros estriba en la correlación existente entre la dureza y la resistencia mecánica, siendo un método de ensayo más económico y rápido que el ensayo de tracción, por lo que su uso está muy extendido.
Hasta la aparición de la primera máquina Brinell para la determinación de la dureza, ésta se medía de forma cualitativa empleando una lima de acero templadoque era el material más duro que se empleaba en los talleres.
Las escalas de uso industrial actuales son las siguientes:
- Dureza Brinell: Emplea como punta una bola de acero templado o carburo de wolframio. Para materiales duros, es poco exacta pero fácil de aplicar. Poco precisa con chapas de menos de 6 mm de espesor. Estima resistencia a tracción.
- Dureza Knoop: Mide la dureza en valores de escala absolutas, y se valoran con la profundidad de señales grabadas sobre un mineral mediante un utensilio con una punta de diamante al que se le ejerce una fuerza estándar.
- Dureza Rockwell: Se utiliza como punta un cono de diamante (en algunos casos bola de acero). Es la más extendida, ya que la dureza se obtiene por medición directa y es apto para todo tipo de materiales. Se suele considerar un ensayo no destructivo por el pequeño tamaño de la huella.
- Rockwell superficial: Existe una variante del ensayo, llamada Rockwell superficial, para la caracterización de piezas muy delgadas, como cuchillas de afeitar o capas de materiales que han recibido algún tratamiento de endurecimiento superficial.
- Dureza Rosiwal: Mide en escalas absoluta de durezas, se expresa como la resistencia a la abrasión medias en pruebas de laboratorio y tomando como base el corindón con un valor de 1000.
- Dureza Shore: Emplea un escleroscopio. Se deja caer un indentador en la superficie del material y se ve el rebote. Es adimensional, pero consta de varias escalas. A mayor rebote -> mayor dureza. Aplicable para control de calidad superficial. Es un método elástico, no de penetración como los otros.
- Dureza Vickers: Emplea como penetrador un diamante con forma de pirámide cuadrangular. Para materiales blandos, los valores Vickers coinciden con los de la escala Brinell. Mejora del ensayo Brinell para efectuar ensayos de dureza con chapas de hasta 2 mm de espesor.
- Dureza Webster: Emplea máquinas manuales en la medición, siendo apto para piezas de difícil manejo como perfiles largos extruidos. El valor obtenido se suele convertir a valores Rockwell.
ENSAYO DE MÓDULO DE CHARPY: El péndulo de Charpy es un péndulo ideado por Georges Charpy que se utiliza en ensayos para determinar la tenacidad de un material. Son ensayos de impacto de una probeta entallada y ensayada a flexión en 3 puntos. El péndulo cae sobre el dorso de la probeta y la parte. La diferencia entre la altura inicial del péndulo (h) y la final tras el impacto (h') permite medir la energía absorbida en el proceso de fracturar la probeta. En estricto rigor se mide la energía absorbida en el área debajo de la curva de carga, desplazamiento que se conoce como resiliencia.
